內容推薦
全球飲料制造商擴大產能并提高一致性
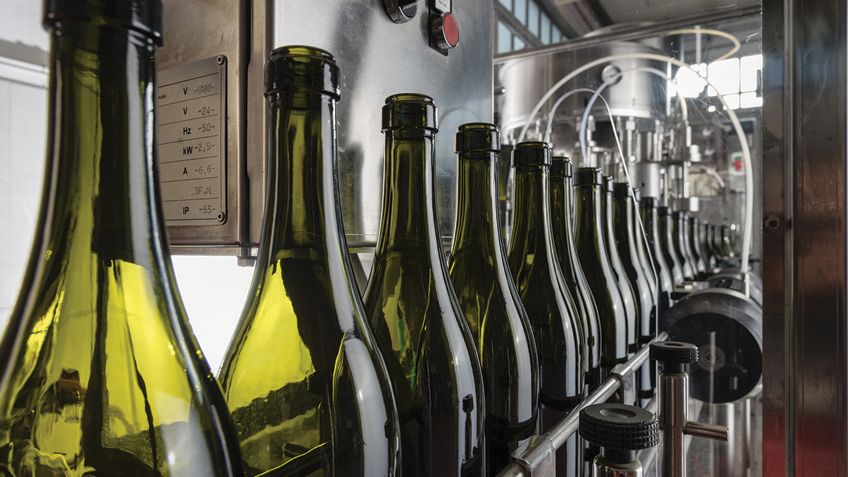
挑戰
- 擴展并移植既有批次系統,以提高飲料生產過程的生產量和一致性
解決方案
- PlantPAx 過程自動化系統 - 這是一種完全冗余的集成系統,它利用服務器虛擬化來提高可用性
- 其中包含可擴展的多領域信息化控制平臺,該平臺具有通信功能和本安型 I/O
- 管理級別的可視化功能可以讓操作員更好地了解過程信息
- 數據管理、性能和可見性以及生產管理軟件可以優化過程和批次控制
成果
- 提高了系統整體效率和生產量
- 改進了過程一致性 - 實現“每個批次的糾正次數不超過一次”的目標
- 提高了系統靈活性 - 根據原材料的差異自動進行調整,并簡化配方的創建過程
- 利用單獨登錄、電子簽名和自動注銷幫助實現更出色的系統安全性
背景
產品安全和一致性對于任何飲料制造過程都是至關重要的。幾十年來,飲料生產商始終依靠非標準批次系統來幫助維護過程質量和生產量。
面對法規的加速推進、技術工人的不斷減少以及市場對提高產品差異化的不斷需求,現在飲料生產商對標準化的要求比以往任何時候都高。
一家跨國蒸餾飲料、啤酒和葡萄酒生產商計劃擴大其伊利諾伊州工廠的產能,他們請求過程設計公司 Barnum Mechanical, Inc. 為其提供一種交鑰匙解決方案。Barnum 聘請 Industrial Automation Group 設計新的控制系統。
總部位于加利福尼亞州莫德斯托的 Industrial Automation Group 專門為食品和飲料行業提供過程控制解決方案。該公司是 Rockwell Automation 認可的系統集成商,并且是控制系統集成商協會 (CSIA) 的認證會員。
挑戰
“提高客戶的過程效率是這家飲料公司的主要目標。”Industrial Automation Group 的項目經理 NinivTamimi 說,“而且,他們還計劃在其系統中添加原料儲存罐、中型的分批儲存罐和裝瓶儲存罐,從而提高總產能?!?br />
工廠進行了大規模擴張,并將接收區的軌道車/卡車工作站和儲油罐增加了大約 75%?;旌鲜乙步洑v了類似的增長情況。在瓶裝過程中,添加了一些罐,而一些現有罐則轉換為“彈性罐”,既可用于瓶裝,也可用于儲存原材料。
“由于他們擴大了運營規模,因此公司計劃移植到一個‘一體化’的批次解決方案?!盩amimi 解釋說,“他們希望安裝一個符合 S88 標準的高效系統?!?br />
ANSI/ISA-88 (S88) 標準針對工業自動化系統中的批次控制提供了一套一致的術語和標準,包括物理模型、程序和配方管理?,F有系統不符合 S88 標準。
“商業數據庫軟件用于配方存儲,并且他們的整個批次系統是使用 Visual Basic for Application (VBA) 代碼和既有 HMI 進行編程的,”Tamimi 說。為了通過現有系統使產品質量達到可接受的水平,工廠通常需要對每個批次實施兩次或三次校正。每一次批次校正的測試時間大約為兩個小時。而且,系統沒有“故障轉移”或冗余功能。
“因此,如果一臺服務器出現故障,系統可能就會中斷兩到四個小時?!盩amimi 說,“除了提高產品質量以外,我們的客戶還需要提高系統可用性?!?br />
最后但同樣重要的是,公司需要提高安全性?,F有系統只有三個登錄名:Operator(操作員)、Supervisor (監督員)和 Administrator(管理員)。所有用戶可輕松共享登錄名的密碼??蛻糁付ㄐ逻^程系統要納入用戶專用的登錄、自動注銷和電子簽名功能。
解決方案
Industrial Automation Group 使用一種基于 PlantPAx? 過程自動化系統的控制解決方案,該系統是 Rockwell Automation 提供的一種現代分布式控制系統 (DCS)。
“利用 PlantPAx 解決方案,我們可以設計一種利用虛擬化等許多新技術的高可用性系統?!盩amimi 解釋說,“實際上,我們選擇了虛擬環境來實施這種應用?!?br />
Rockwell Automation 通過 VMware? Ready 認證軟件來支持虛擬化,并建議使用服務器虛擬化和 VMware vSphere?(在處理運行時生產應用時)。實現服務器虛擬化后,無需依賴于完整的主機操作系統 (OS),并且還為關鍵應用提供一個更加穩定的環境。
新系統包括一個可擴展的多領域信息化控制平臺,該平臺將過程和離散控制與通信和本安型 I/O 相結合。這個完全冗余的系統可控制加工區域的應用以及原位清洗 (CIP) 成套設備。此外,還集成了遠程控制,以進行危險的 1 類 1 區處理。在控制室和批處理室建立了操作員工作站。此外,還在控制室建立了工程師站,以實現過程的實時優化。
另外,PlantPAx 系統還包括管理級別的可視化功能,可以讓操作員最充分地了解過程信息。數據管理、性能和可見性以及生產管理軟件提供過程控制和批次控制。
為了使工廠在整個升級過程中盡量保持正常運轉,Industrial Automation Group 分階段實施該系統。首先是散裝液體接收區域,包括新的卡車和軌道站點以及新的散裝儲存罐。還對這些資產使用 CIP 序列。
接下來,添加了新的批處理系統。為了實施該系統,工作人員重新創建了 120 個原配方。由于工廠擴建以及系統中增加了新資產,在此過程中修改了材料添加順序,以便在確保質量的前提下縮短批處理時間。
“嚴格的測試和質量控制極其重要?!盩amimi 說,“我們必須先證明新系統可以運行現有配方,然后才能淘汰舊系統?!碑敵跗诘墓S驗收試驗 (FAT) 結束后,團隊在兩個星期的停機期內集成了新的控制系統。然后,對系統進行進一步測試,并根據需要調整參數和配方。
成果
“工廠的總體生產量和一致性得到了提高?!盩amimi 說,“而且,公司可以使用批次系統更輕松地添加新配方,因為大多數操作和許多單元過程都是共享的。”
為了進一步簡化配方的開發過程,系統允許根據操作員輸入的信息或其他定義的變量實現動態優先排序。由于該批次軟件具有材料管理功能,因此如果同一種材料位于不同的罐中,則無需重新編寫配方。
在調試階段,Industrial Automation Group 幫助該飲料公司引進了 50 種新配方。
該系統還改進了 CIP 報告。每個 CIP 周期結束后,系統會跟蹤所有排序情況并自動生成報告,以便在運行下個批次之前記錄恰當的清潔程序。
此外,該系統還有助于確保產品的一致性。
“進入系統的原料的屬性未必與配方中所定義的屬性完全相同。”Tamimi 解釋道,“在這種情況下,我們可以更新系統中的參數,它會自動調整每個配方中的原料含量。”
部署好 PlantPAx 系統后,該飲料工廠實現了他們的“每個批次的糾正次數不超過一次”的目標。
最后,系統通過使用單獨的登錄名和電子簽名提高了安全性。系統還強制 15 分鐘自動注銷,而對于所有關鍵項目,則要求重新輸入憑證。
發布時間 2014年8月1日